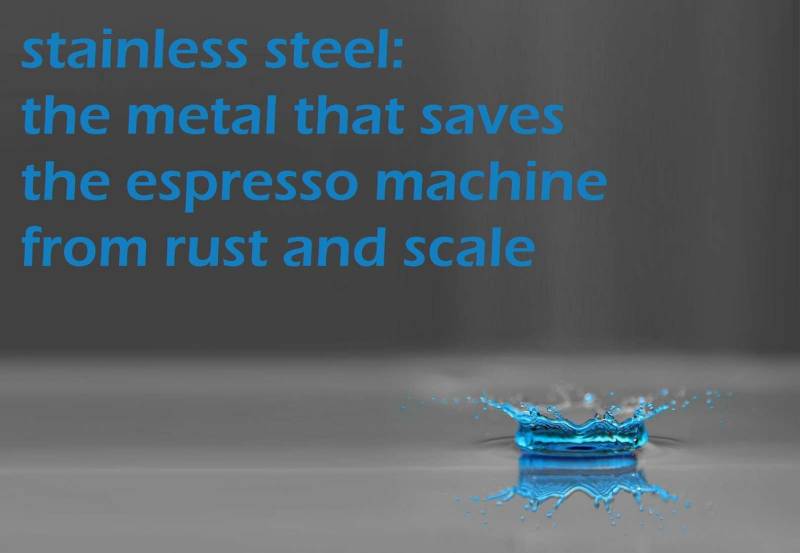
Stainless steel saves the espresso machine from corrosion, rust and scale due to its 'passive behaviour'
Anyone with an espresso machine knows the difference between a well-maintained machine with no rust or scale deposits and a dirty and crusted machine. Even if he had noticed it by himself, the scowls of consumers after their first taste of the espresso should be quite eloquent.
Inside the machine, corrosion and limestone formations are of the electrochemical process, natural and irreversible, due to the slow and continuous consumption of the metal by the water. Consequences are the worsening of the physical properties of the various components, the accelerated wear of the machine and a definitely not pleasing result in the cup.
The electrolytic corrosion is a process caused by an oxidation reaction (in the anode) and reduction (in the cathode): a metal or alloy with a low carbon content have generally an active electrochemical behaviour and is a positive electrode which responds to the reaction medium (water is a good ionic conductor). While oxidizing, the iron cations leave their sites to spread into the environment, while the electrons remaining in the structure are moving on the cathodic area, allowing the formation of hydroxyl ions and then making the cathodic area (the water) alkaline.
Hence 2 different types of reactions, according to water hardness (calculated from the concentration of calcium salts, magnesium salts and dissolved minerals) in which the metal is immersed:
- Excessively high hardness level: the presence of high quantities of minerals in the water facilitates the process through which the hydroxyl ions, in contact with ferrous ion, form a ferrous hydrate which, in turn, come into contact with oxygen triggering a process of oxidation and becomes what is commonly called rust (which is basically a change of iron status, from solid to dusty) that, slightly soluble, precipitates on the metal. The water electrical conductivity, and therefore the corrosion rate, increases as the amount of dissolved salts raises.
- Excessively low hardness level: when the demineralized water (status 'neutral') comes in contact with the ferrous ions that diffuse from the anode, tends to increase its level of acidity, and if the ferrous material presents the areas of oxidation, the water attacks the oxide layer, dissolving. The dissolved oxide will lead to the first scale formation.
It must also be remembered that it is difficult to work in an isolated environment, and that the oxygen and the carbon dioxide present in the air melt quickly in the water, facilitating the process of oxidation of the iron to rust.
The water input to the espresso machine must therefore have the correct level of hardness to prevent rust or calcification: a water too hard leads to the formation of rust, while a water with less salts (therefore with a smaller number of charges free) dissolved tends to slow down the corrosion process, but simultaneously accelerates the formation of lime dissolved in the water.
To regulate water quality popular systems are water softeners and reverse osmosis system.
For those who have difficulty in regulating the quality of water input, is however advised to replace the components of the coffee machine realized with poor carbon iron alloys and replace them with components made of noble metals or alloys, such as steel, the copper, aluminum or brass.
These alloys, and in particular in stainless steel, are characterized by a passive electrochemical behaviour. The protective action of the passivation, the process that leads to the formation of a continuous and oxides adhering to the surface of the material film (a few microns), inhibits the anodic process in such a way that the corrosion rate becomes negligible.
Those who wish to proceed more drastically or would give new life to a historic machine of value, may decide to remove the surface oxide layer contacting a specialized company, who will remove the surface layers of the metal through an chemical or electrolytic operation called pickling and that is carried out with acid or alkali solutions. This process is used for the industrial processing of hot rolled copper, brass and steels with low carbon, to make the metal surface porous before proceeding to other treatments.